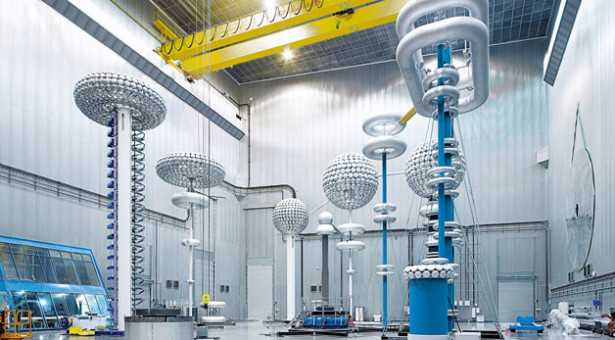
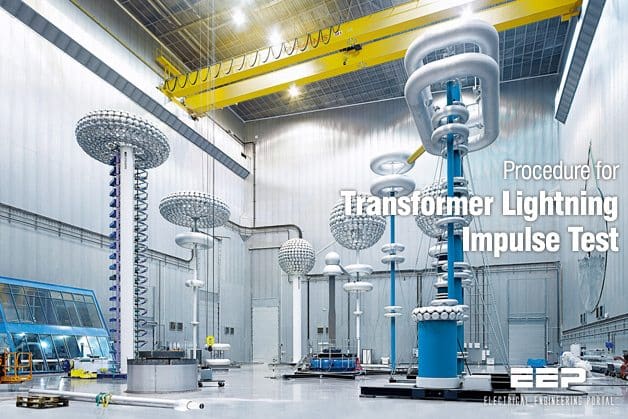
Purpose of the test
The purpose of the impulse voltage test is to secure that the transformer insultations withstand the lightning overvoltages which may occur in service.
Testing equipment
Impulse generator

Where:
- C1 – Impulse capacitor
- Rc – Charging resistor
- Rs – Series resistor
- Ra – Low-ohmic discharging resistor for switching impulse,
- Rb – High-ohmic discharging resistor for switching impulse
- F1…Fn – Main spark-gaps,
- Fal…Fan – auxiliary spark-gaps
The impulse generator design is based on the Marx circuit. The basic circuit diagram is shown on Figure 1 above. The impulse capacitors Cs (12 capacitors of 750 nF) are charged in parallel through the charging resistors Rc (45 kΩ) (highest permissible charging voltage 200 kV).
When the charging voltage has reached the requider value, breakdown of the spark-gap F1 is initiated by an external triggering pulse. When F1 breaks down, the potential of the following stage (points B and C) rises. Because the series resistor Rs is of low ohmic value compared with the discharging resistor Rb (4.5 kΩ) and the charging resistor Rc, and since the low-ohmic resistor.
Ra is separated from the circuit by the auxiliary spark-gap Fa1, the potential difference across the spark-gab F2 rises considerably and the breakdown of F2 is is initiated. Thus the spark-gaps are caused to break down in sequence.
This arrangement is necessary in order to secure the functioning of the generator.
The required voltage is obtained by selecting a suitable number of seriesconnected stages and by adjusting the charging voltage. In order to obtain the necessary disscharge energy parallel or series-parallall connections of the generator can be used. In these cases some of the capacitors are connected in parallel during the discharge.
Max. test voltage amplitudes: 2.1 MV lightning impulse. 1.6 MV switching impulse.

Where:
- Cr – Resulting impulse capacitance
- Rsr – Resulting series resistance
- Rar – Resulting discharge resistance
- Lr Lp – Stray inductances
- Ci – Input capacitance of transformer
- Li – Transformer inductance
- C1 – Capacitance of voltage divider
- F1 – Spark gaps of impulse generator
- F2 – Calibration sphere gap
- R2 – Protective resistor.
The front time can be calculated approximately from the equation:
T1 ≈ 2,5 · Rsr · (Ci + C1) (formulae 1)
and the time to half value from the equation:
T2 ≈ k · √(Li · Cr) (formulae 2)
The factor k depends on the quantities Rsr, Rar, Li and Cr. In practice the testing circuit is dimensioned according to experience.
Voltage measuring circuit
The impulse shape and the peak value of the impulse voltage are measured by means of an oscilloscope and a peak voltmeter which are connected to the voltage divider (Figure 3). The measuring range can be changed by shortcircuiting part of the high voltage capacitors or changing the low voltage capacitor of the divider.

Where:
- E – Damped capacitive voltage divider
- W – Measuring cable (= wave impedance = Rp)
- P1 – Oscilloscope
- P2 – Peak voltmeter
- Rp – Terminal resistance of the measuring cable
- R1 – Damping resistor of voltage divider
- C1 – High voltage capacitor of voltage divider
- C2 – Low voltage capacitor of divider.
The measuring circuit is checked in accordance with the standards (formulae 2) and (formulae 3). If necessary the sphere-gap calibration of the measuring circuit can be performed in connection with the testing according to the standard (figure 4 below).
Transformer testing and fault detection connections
The lightning impulse test is normally applied to all windings. The impulse testsequency is applied successively to each of the line terminals of the tested winding. The other line terminals and the neutral terminal are earthed (singleterminal test, Figure 4a and 4b).

Where:
- a, b – 1-terminal testing
- c – 3-terminal testing
- d – 2-terminal testing
- e – test with transferred voltages
- f – neutranl terminal testing
When testing low voltage windings of high power the time to half-value obtained is often too short. However, the time to half-value can be increased by connecting suitable resistors (Ra in Figure 4b) between the adjacent terminals and earth.
A delta-connected winding (and star-connected winding, unless the neutral is available) is also tested with an impulse test-sequence applied to the line terminals of the tested winding connected together, while the other windings are earthed (three-terminal test, Figure 4c).
For delta-connected windings the single and three-terminal testings can be combined by applying the impulse to two line terminals at a time, while the other line terminals are earthed (two-terminal testing, Figure 4d). In this case two phases are simultaneously tested in a single-terminal connection and one phase in a test connection corresponding to three-terminal testing.
The two- and three-terminal testings are not included in the standard, but they can be done if it is so agreed.
When the low voltage winding cannot in service be subjected to lighting overvoltages from the low voltage system (e.g. step-up transformers, tertiary windings) the low voltage winding may (by agreement between customer and manufackturer) be impulse tested simultaneously with the impulse tests on the high voltage winding with surges transferred from the high voltage winding to the low voltage winding (Figure 4e, test with transferred voltages).
The resistance shall not exceed 5000 Ω. The neutral terminal is normally tested indirectly by connecting a high-ohmic resistor between the neutral and earth (voltage divider Ra, Ru) and by appluying the impulse (Figure 4d) to the line terminals connected together.
For fault detection in single-terminal and two-terminal tests the neutral of star-connected windings are earthed via a low-ohmic resistor (Ru). The current flowing through the detection resistor during the test is rocorded by means of an oscilloscope. Evidence of insultaion failure arising from the test would be given significant discrepacies between the calibration impulse application and the full voltage applications in recorded current wave-shapes.
Certain types of faults give rise to discrepancies in the recorded voltage wave-shapes as well.
For fault detection in three-terminal tests and tests on the neutral terminal the adjacent winding is earthed through a low-ohmic resistor. The fault detection is then based on recording the capacitive current which is transferred to the adjacent winding.
Lightning Impulse Test on Transformer (400KV/15KV, 160MVA)
Cant see this video? Click here to watch it on Youtube.
Reference // Testing of power transformers – ABB
The post Procedure for Transformer Lightning Impulse Test appeared first on EEP - Electrical Engineering Portal.